Metal surface treatment
Fine shot peening
Fine shot peening process
Fine shot peening is an improvement of the surface of the material to increase the strength of the surface by firing small spherical particles. The diameter of the diameter from 0.04-2 mm enters the surface of the object at a high speed of more than 100 m / s by various surface treatment particles depending on the application requirements. The hardness of the particles used must be higher than the surface treatment material. The surface treatment by spraying with fine particles creates a hole in the surface of the material, indicating permanent deformation. This will result in the surface of the material having a higher hardness value. And the residual compressive stress occurs As a result, the material that has gone through this process has a higher bending fatigue. And the bending strength of the material is increased Including the effect of the hardness that increases, it will help to prevent crack even more better. Which can help extend the service life of the material. Compared to other surface treatment processes, the finer particle blasting has more advantages: Able to adjust the surface around holes or grooves. Does not change or make any slight change to other properties of the material. And take more time to adjust the skin and cost Today, this process is used in many different industries, such as the automotive industry. Aircraft industry, for example, to extend the life of equipment such as shaft, gear or even aircraft turbine blade
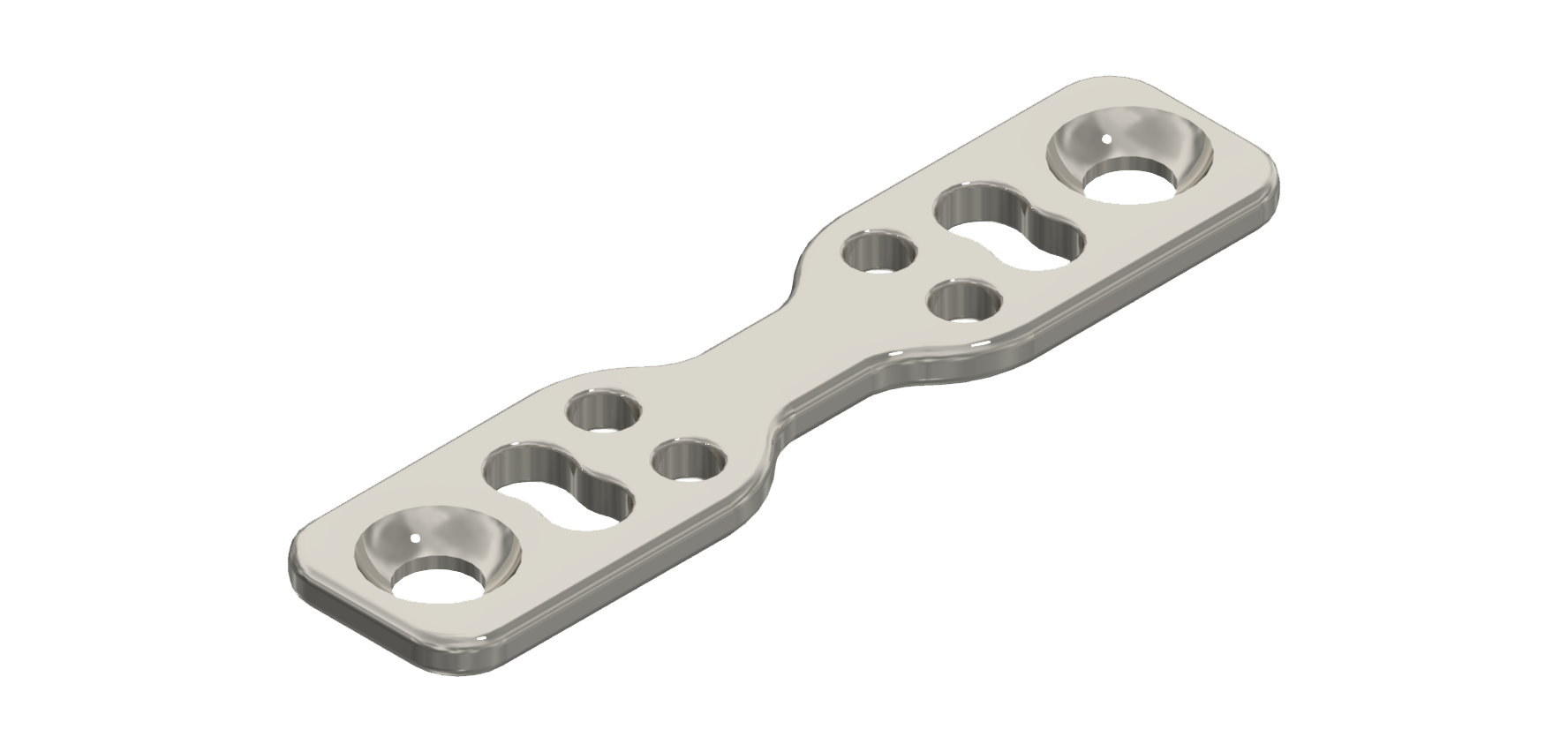
Company knowledge
Currently, the company collaborates with universities to continuously study the influence of various parameters of fine particle emission processes. Both types of particles Particle size Shot pressure, blast distance, shot blasting and much more have been studied in a wide range of materials such as stainless steel (SUS316L), titanium alloy (Ti6Al4V, Ti6Al7Nb). Strength to various materials Which has a very high energy will cause permanent deformation to occur. As a result, the grain structure of Wat Su has changed. Leading to a change in the hardness of the material in that area And when the image is restored, the image cannot be restored completely, thus creating a residual compression in that area And increased hardness near the surface As a result, the material is able to handle the bending force better. Better wear resistance Until leading to a long service life that is several times longer Nowadays, the company has important knowledge of this process such as the particles used in the shot blasting. Time required to fire Including many more spraying conditions This will affect both the mechanical and physical performance of the material. The company has studied the increase of surface hardness as shown in Figure 1, the residual compressive stress (Figure 2) and many other values.
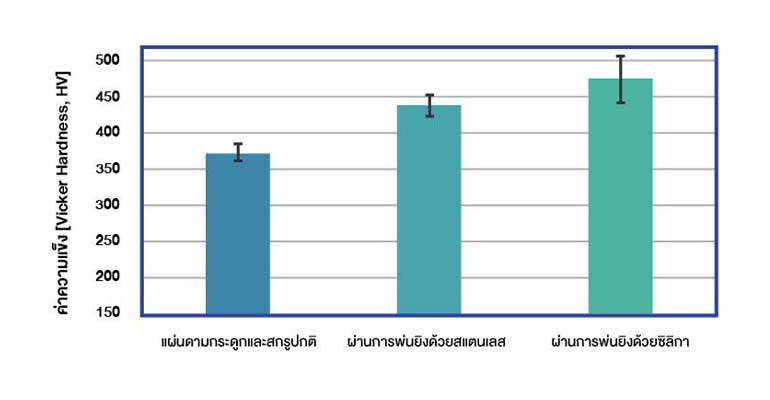
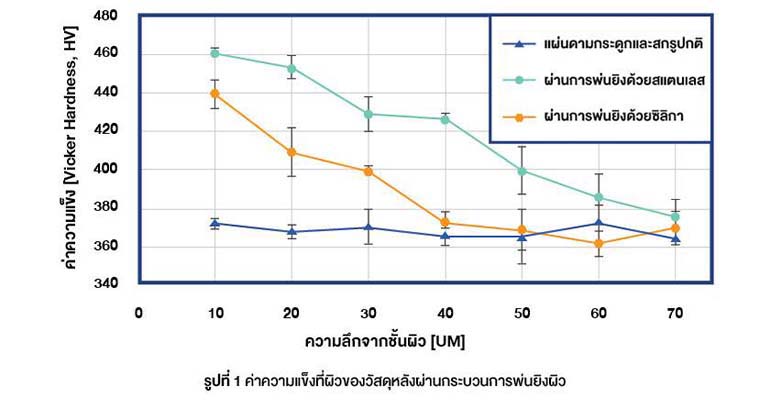
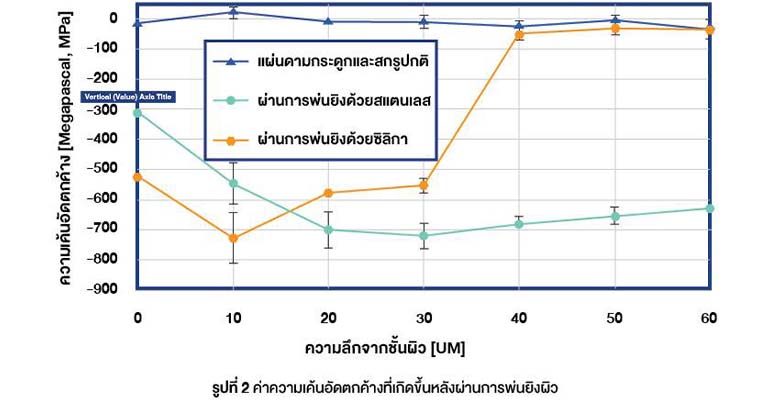
Advantages and Limitations of this process
Advantages
Does not change the main properties of materials
• Can control the surface flatness value.
• No change in workpiece size
The enhanced skin properties did not change when the skin peeled off.
• Use the fast timing
• Can be performed on smaller parts.
Restrictions
Must have an understanding of selecting the variables that will be used in the surface treatment.
• There are more than 1,000 particle types and sizes, so knowledge is required to select suitable particles for their application.
• The controllers must have a certain level of expertise to control the effectiveness of the process.
• The materials that are sprayed will produce different effects. Depending on the treasure of that temple The thrower has to be continuously researched for new materials.
Engineering applications
Gears of motor vehicles or machinery (Gear) to prolong their service life, prevent the wear of gear teeth
Automotive tweezers (Lift spring) to prolong service life by creating residual compressive stress to obtain flexural fatigue strength.
propellers in both aircraft and power plant parts (Turbine blades) to prolong the service life from impact with wind or various pressure and reduce the coefficient of friction on the blade surface.
Shaft to prolong the service life from various loads.
Medical device to prevent fracture, damage and prolong life. Use
Metal structure to increase the strength of various metals in the structure to prevent fracture. Or damaged by shock or impact.
Heat exchanger to increase the surface area contact with heat to create a very good heat pouring. More
Pipe to speed the fluid flow from reducing the friction coefficient at the surface of the pipe.